74chlngrTT5.9
Well-Known Member
Ok, Time to start writing instead of just lurking. I have had this car since 1984.
I have also started a thread on another forum but here feels more appropriate for the knowledge and feedback you all have here.
The build is to be primarily focused on the go parts and later turning to the body and paint.
I have been following some of the full restorations on here and I can only imagine the amount of detailed work that is required to complete them.
Mine is a California car that has been garaged most of its life. It has always been drivable. Only a single front fender and door have been patched and repainted on the car. This happened before I got it back in 84. The hood was painted also because it is a later addition to the car. All else is still the original paint. Many places it is so thin you can see through it. One small patch of rust in lower rear quarter. In front of wheel well from a plugged drain hole :-(. Premise of this build is to add twins with dual air to air IC's. Two things I am fairly retentive about with the car are. #1 is that if I cannot build it without bastardizing the sheet metal then it will not happen. The second item is that with twins all is visually symmetrical. Car started life as a very low end base model. 318, 3spd stick and power nothing. So changing the mechanicals doesn't mean much to me. Car now has a 360 LA with the A833 four speed (yes Pistol grip) Power steering added (tuff wheel too). I have gained a lot of weight over all the years of owning this and am still only up to a buck 70. PS is way needed... Also added Power brakes to the car way back when. Plans for now are: 2001 5.9 motor. Already have good low mileage one that will get a refurb when the time comes. Reasoning for the later model 5.9 is that the P/S pump and alternator are mounted much closer to the motor. The WP is also somewhere around 2 inches shorter. The shorter W/pump is what ended up allowing my plan to work being retentive about the sheet metal.
Eddy heads -Need/want-
T3/4 Eb@y turbos -Have- 4 speed to remain (for now).
M1 intake. I will be going fuel injection. Probably blow through carb with the initial startup when motor is swapped in.
Megasquirt most likely. LS coils with crank and cam triggers probable Fuel system not decided.
Custom tank with internal pump. Not interested in hearing the pump drone on.
Probably Hotchkiss frame connectors.
All the hot side piping to be SS. welded by me. Cold side to be as mentioned above dual intercoolers with custom tanks. Aluminum piping also welded by me.
Brakes to be converted to Hydroboost Car will also get air added. Many of the items listed are already partially started. I tend to bounce around a lot. Start a project. let it sit... think about it for awhile... let it sit... figure it out and then jump on it until the next thought session. Goals for the motor are to reach around 550 bhp. This is a home built project and it will be a 100% street car. All items are subject to change based on funds and input from the many members that are sure to know more than me.
Main item is car will not be out of commission for any long duration. I also have a 68 Mustang (N/A) that was down for 17 years. Ain't gonna happen again...
I will be cutting and pasting for a bit to get this up to current day.
Hope this was posted in the correct section thanks
Mike.
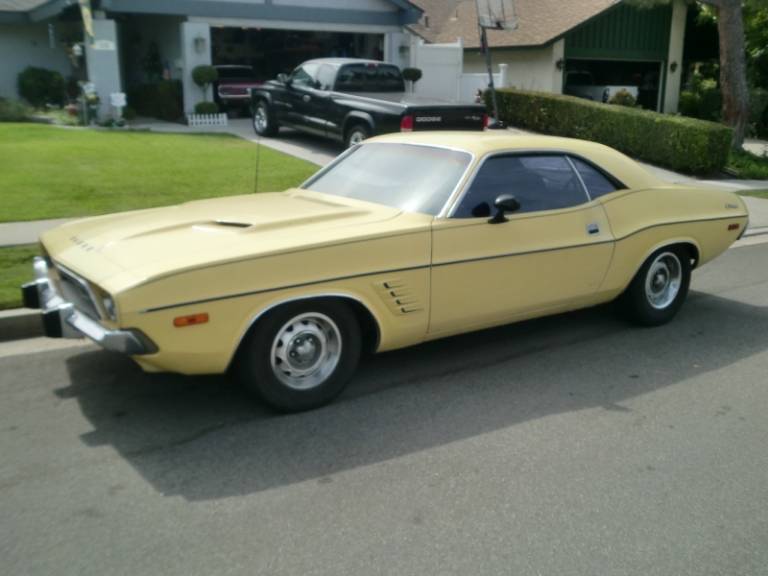
I have also started a thread on another forum but here feels more appropriate for the knowledge and feedback you all have here.
The build is to be primarily focused on the go parts and later turning to the body and paint.
I have been following some of the full restorations on here and I can only imagine the amount of detailed work that is required to complete them.
Mine is a California car that has been garaged most of its life. It has always been drivable. Only a single front fender and door have been patched and repainted on the car. This happened before I got it back in 84. The hood was painted also because it is a later addition to the car. All else is still the original paint. Many places it is so thin you can see through it. One small patch of rust in lower rear quarter. In front of wheel well from a plugged drain hole :-(. Premise of this build is to add twins with dual air to air IC's. Two things I am fairly retentive about with the car are. #1 is that if I cannot build it without bastardizing the sheet metal then it will not happen. The second item is that with twins all is visually symmetrical. Car started life as a very low end base model. 318, 3spd stick and power nothing. So changing the mechanicals doesn't mean much to me. Car now has a 360 LA with the A833 four speed (yes Pistol grip) Power steering added (tuff wheel too). I have gained a lot of weight over all the years of owning this and am still only up to a buck 70. PS is way needed... Also added Power brakes to the car way back when. Plans for now are: 2001 5.9 motor. Already have good low mileage one that will get a refurb when the time comes. Reasoning for the later model 5.9 is that the P/S pump and alternator are mounted much closer to the motor. The WP is also somewhere around 2 inches shorter. The shorter W/pump is what ended up allowing my plan to work being retentive about the sheet metal.
Eddy heads -Need/want-
T3/4 Eb@y turbos -Have- 4 speed to remain (for now).
M1 intake. I will be going fuel injection. Probably blow through carb with the initial startup when motor is swapped in.
Megasquirt most likely. LS coils with crank and cam triggers probable Fuel system not decided.
Custom tank with internal pump. Not interested in hearing the pump drone on.
Probably Hotchkiss frame connectors.
All the hot side piping to be SS. welded by me. Cold side to be as mentioned above dual intercoolers with custom tanks. Aluminum piping also welded by me.
Brakes to be converted to Hydroboost Car will also get air added. Many of the items listed are already partially started. I tend to bounce around a lot. Start a project. let it sit... think about it for awhile... let it sit... figure it out and then jump on it until the next thought session. Goals for the motor are to reach around 550 bhp. This is a home built project and it will be a 100% street car. All items are subject to change based on funds and input from the many members that are sure to know more than me.
Main item is car will not be out of commission for any long duration. I also have a 68 Mustang (N/A) that was down for 17 years. Ain't gonna happen again...
I will be cutting and pasting for a bit to get this up to current day.
Hope this was posted in the correct section thanks
Mike.
Last edited: